Enhancing Performance with Specialized Packaging Equipment Repair Services
Enhancing Performance with Specialized Packaging Equipment Repair Services
Blog Article
Tailored Product Packaging Equipment Repair Service Provider to Match Your Unique Service Demands
In today's affordable market, services must guarantee their product packaging procedures run effortlessly, and customized repair work services for devices are critical in accomplishing this. This conversation intends to discover the nuanced advantages of tailored repair service methods.
Comprehending Your Equipment Demands
To efficiently address the repair and maintenance of product packaging equipment, it is vital to obtain an extensive understanding of your tools needs (packaging equipment repair services). This includes assessing the certain types of machinery in use and recognizing their roles within your production line. Identifying these elements enables you to prioritize upkeep jobs and designate sources effectively, decreasing downtime and ensuring smooth procedures
A thorough supply of your devices, consisting of make, design, age, and maintenance history, develops the cornerstone of this understanding. This data promotes notified decision-making pertaining to upgrades and repair services, guaranteeing that interventions are both cost-effective and prompt. In addition, understanding the functional needs positioned on each tool assists in predicting damage patterns, thus allowing more accurate organizing of preventative maintenance.
Teaming up with well-informed professionals who can offer professional evaluations and referrals is likewise necessary in improving your tools administration method. Inevitably, a comprehensive grip of your equipment requires not just maximizes efficiency but additionally prolongs the lifespan of your equipment, safeguarding your investment.
Benefits of Personalized Repair Service Solutions
Personalized repair service solutions use a customized strategy to repairing and keeping packaging equipment, making sure options that fit the unique needs of each business. This bespoke strategy offers myriad advantages, boosting operational efficiency and decreasing downtime. By understanding the certain equipment and procedures of a firm, personalized services can deal with concerns better than generic remedies, guaranteeing that fixings are straightened with operational objectives and operations characteristics.
Additionally, these services assist in better source administration. Tailored repair strategies assist anticipate maintenance demands, allowing companies to allot resources a lot more effectively and minimize unanticipated costs. This positive technique not just prolongs devices life-span but also optimizes efficiency, stopping constant breakdowns and cultivating a more reliable manufacturing atmosphere.
As packaging technologies development, having a fixing solution attuned to a company's one-of-a-kind configuration makes sure quick adaptation to new devices and procedures. Additionally, personalized solution cultivates a better relationship with repair work companies, making sure quicker action times and more effective interaction, eventually leading to improved service quality and business development.
Key Parts of Tailored Solutions
A well-crafted customized solution for product packaging equipment repair is developed upon a number of critical components that guarantee effectiveness and dependability. First of all, a comprehensive evaluation of the tools is vital. This involves detecting the origin of any kind of functional issues and comprehending the certain requirements of the machinery, which prepares for developing a precise fixing strategy.
Second of all, the usage of top quality, suitable parts is critical. Choosing components that line up with the original equipment requirements not only boosts functionality however also lengthens the life-span of the equipment. This attention to detail reduces the threat of future failures and guarantees seamless operation.
Another vital part is the implementation of a customized upkeep strategy. packaging equipment repair services. Precautionary actions and regular evaluations customized to the equipment's one-of-a-kind requirements can substantially minimize downtime and improve performance
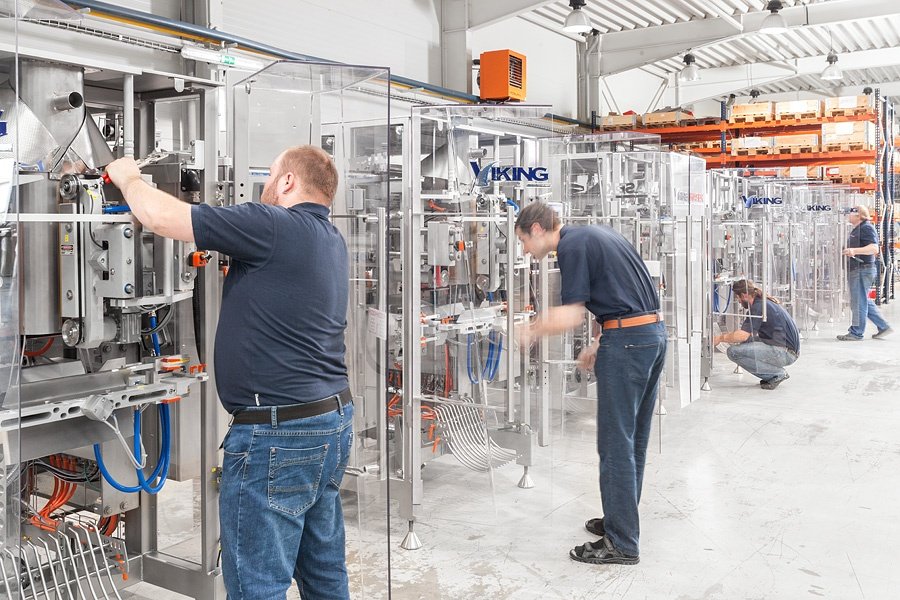
Integrating these aspects into a customized repair work option not only addresses instant problems but also offers long-lasting benefits, boosting overall productivity and cost-effectiveness for businesses.
Selecting the Right Solution Service Provider
Selecting the ideal company for packaging devices repair service read here is a critical decision that can dramatically influence an organization's functional efficiency and price management. A reliable provider makes sure prompt fixings and maintenance, decreasing downtime and avoiding possible manufacturing delays. When selecting a supplier, businesses need to think about a number of essential factors to ensure they select a companion who straightens with their details needs.
To start with, proficiency and experience in handling similar equipment are important. A company with a tried and tested performance history in the packaging industry can offer click over here now understandings and options tailored to one-of-a-kind service obstacles. References and study from previous customers can supply important proof of their abilities.
Secondly, assess the copyright's responsiveness and availability. packaging equipment repair services. An optimal companion should offer versatile solution alternatives, including emergency repair work solutions, to attend to urgent demands quickly. This ensures minimal interruption to operations and keeps efficiency degrees
Furthermore, think about the range of services supplied. A comprehensive supplier should not just supply repair services however also preventive maintenance and technical assistance. This alternative technique can improve procedures and foster long-lasting partnerships.
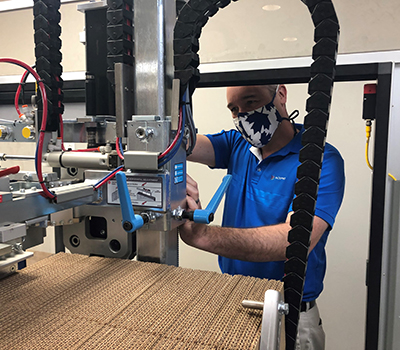
Maximizing Tools Life-span
Effective tools maintenance approaches are as crucial as choosing the appropriate service supplier when it comes to making best use of the life-span of packaging tools. Such positive measures ensure that equipment functions at peak efficiency, thus alleviating the risk of costly downtime.
Furthermore, investing in training for your technological team can significantly impact the longevity of the equipment. Experienced personnel can identify possible concerns early, enabling speedy corrective actions. This not only improves the life expectancy of the tools but additionally enhances total efficiency. Maintaining comprehensive maintenance records is crucial. These logs give insights into recurring concerns and aid in planning future maintenance tasks a lot more successfully.

Conclusion
Tailored packaging tools fixing solutions play a crucial duty in improving operational efficiency and reducing downtime by straightening repair services with certain workflow characteristics. These tailored services utilize high-quality, suitable parts and proactive upkeep strategies to prolong devices life expectancy and optimize efficiency.
In today's affordable market, services should guarantee their product packaging operations run perfectly, and tailored fixing solutions for devices are pivotal in achieving this.To properly resolve the fixing and maintenance of product packaging devices, it is vital to get a detailed understanding of your devices needs.Personalized discover this repair service services use a tailored method to preserving and fixing packaging devices, making sure remedies that fit the one-of-a-kind needs of each company.Reliable tools upkeep approaches are as vital as picking the best service company when it comes to maximizing the life-span of packaging devices.Tailored product packaging equipment fixing services play an essential function in boosting operational efficiency and lowering downtime by aligning repair services with details operations dynamics.
Report this page